JH Acidification NH4+ for pigs
Why choose JH Acidification NH4 +?
- Added value for the farmer – Added value for the climate
- The only technology with emission reductions from the pig units, the storage tank and on application to the fields
- Reduced ammonia evaporation – 64 %
- Reduced odor emission – 51 % with JH SmellFighter
- Reduced methane gas emission
- Reduced nitrous oxide emission
- Reduced hydrogen sulphide emission
- Reduced CO2 emission
- Reduced nitrate leaching from the fields to the aquatic environment
- Reduced dust in the pig unit
- Significantly better work environment for the staff
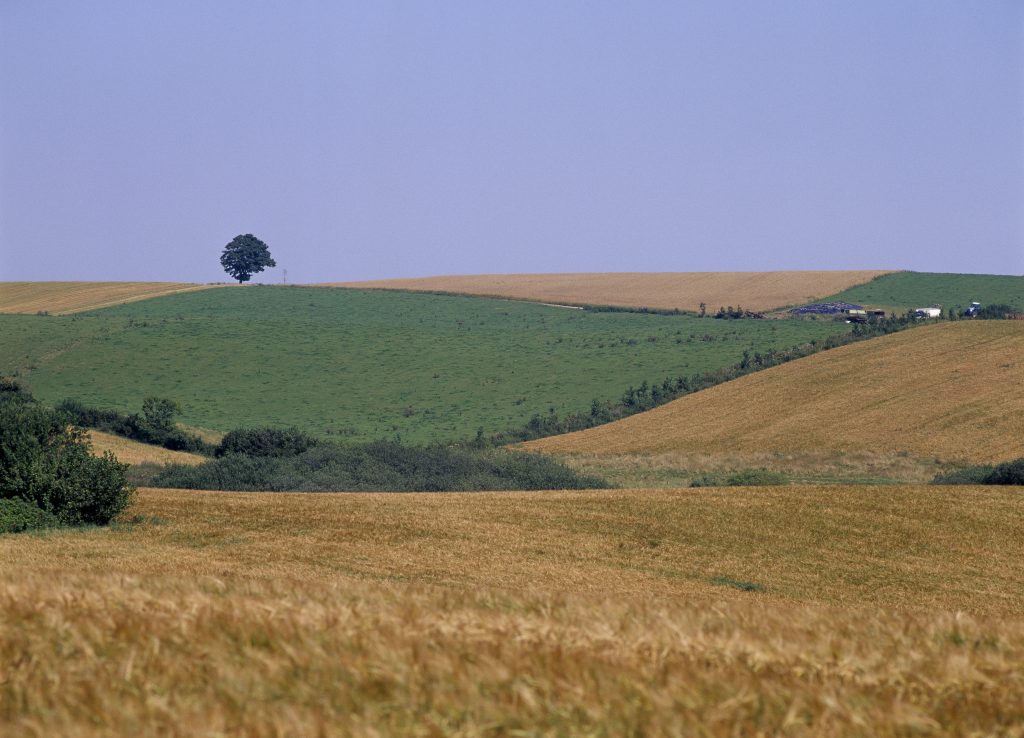
Why choose JH Acidification NH4 +?
- Nitrogen from acidified slurry is taken up faster by crops
- Acidified slurry covers the sulfur requirements of crops
- Better feed utilization and weight gain
- Acidified slurry reduces the need for manganese spraying
- Hose lay-out reduces tramline compaction
- Less crop damage when applied by hose in relation to injection
- Slangeudlægning giver færre kørespor end nedfældning
- Acidified slurry with higher and stabilized nitrogen content is easier to sell on slurry agreements
Why choose JH Acidification NH4 +?
- Proven and verified technology for slurry acidification
- Fully automatic slurry handling – savings on labour costs
- The technology can be used in new and most existing pig units
- The technology can be adapted to the size of production
- Nitrogen is retained in acidified slurry – savings on purchase of fertilizer
- Improved animal welfare
- Significantly less flies in the pig unit
- Fully slatted floors provide for minimal cleaning in the pigpens
- Sulphuric acid does not damage concrete and inventory in the pig unit
Installation
- Double-wall sulfuric acid tank
- PLC for control and monitoring of the acidification process
- The system is installed directly at the barn
- A process tank where the sulfuric acid is mixed with the slurry
Technical well
- Distributes the slurry with the help of pneumatic valves
- 2 versions
- 4 valves or 6 valves
- Max. 2 technical wells per system
The Process
- The slurry is pumped directly from the barn to the process tank, where the sulfuric acid is added automatically. The dosage is controlled by a pH-sensor.
- The treated slurry is automatically pumped to the storage tank and back into the barn. Part of the treated slurry is pumped back into the slurry channels in the barn.
- With treated slurry in the slurry channels, emission of environmentally harmful gasses is reduced, benefitting the environment, as well as animal- and human-health in the barn.
Verified technology
- Test and verification of environmental technology in the agricultural sector
- To strengthen a well-functioning international market for environmental technology
- Multinational cooperation Denmark, The Netherlands and Germany
Links:
Vera Statement